-
- Flexibility to receive streaming data from sensors gateways
- Real-time monitoring of asset condition and performance
- Identifies the main root cases of failure (e.g., abnormal fluctuation in pressure)
- Provides short term and long-term prediction including weekly, monthly; and quarterly.
- Tests millions of scenarios to provide optimal maintenance schedule.
- Offers high scalability to seamlessly add more production sites and machines.
- Easy deployment, web-based management and visualization
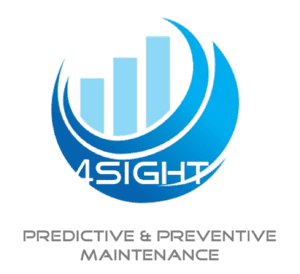
Predict Failure, Minimize Downtime and Build a Smart Maintenance Schedule
About 4Sight
4Sifght is an AI-driven predictive and prescriptive maintenance solution which helps industrial organizations gain the highest return on critical assets by improving reliability, performance, and safety. The solution offers asset-intensive organizations a tool to reduce equipment downtime, increase reliability, and improve performance while reducing operations and maintenance expenditures.
Why 4Sight
The ability to predict the remaining useful life of a part or an asset based on real-time and historical data gives organizations an unprecedented way to manage and optimize their maintenance resources. Investing in predictive maintenance is worth it as it brings significant value to the business by reducing unnecessary maintenance costs as well as regulating the machine’s life, physical conditions, and work efficiency.
Unique Edge
4SIGHT presents a departure from traditional condition monitoring which focuses on instantaneous health-check to a tool that provides early detection of failure short and long term. The prescriptive feature of 4SIGHT provides the optimal maintenance schedule with frequency low enough to prevent unplanned reactive maintainance without incurring costs associated with redundant preventive measures.
What Makes 4Sight Best-in-Class
Maintainance Automation
Why is 4SIGHT Important for Organizations
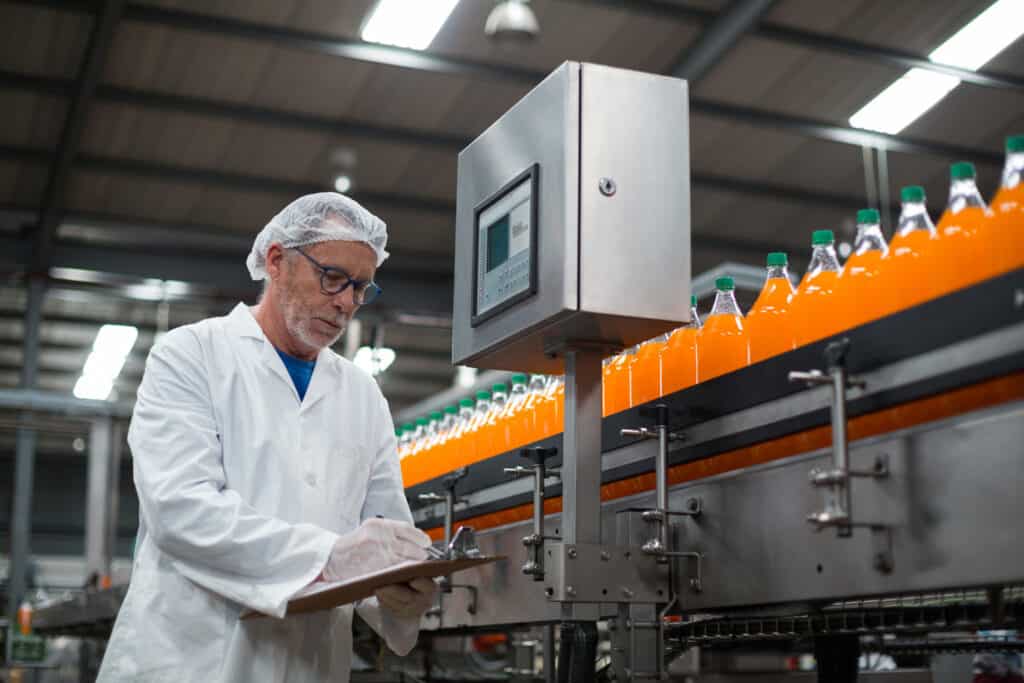
How Does it Work
4Sight in Action
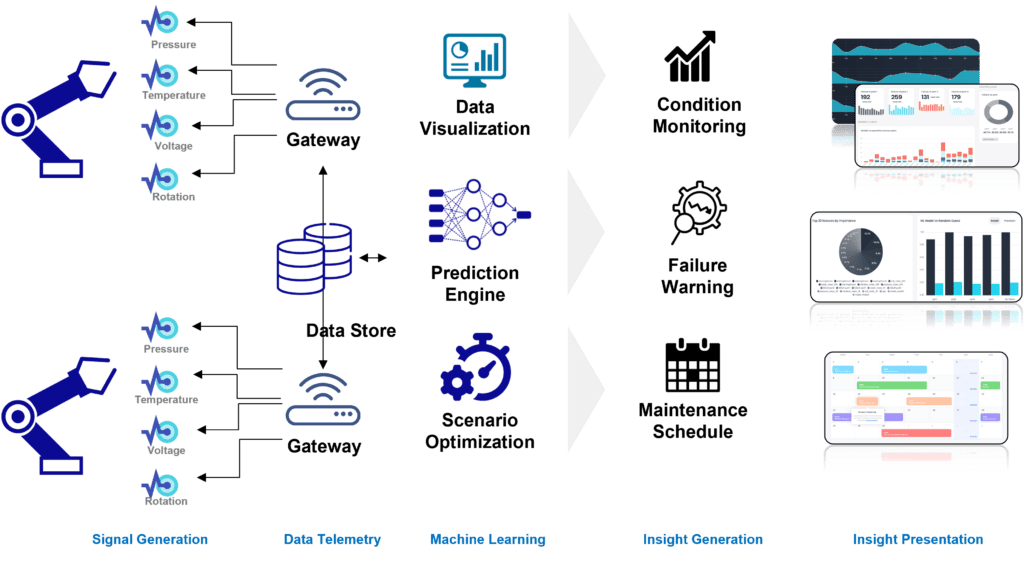
Robust and Scalable !
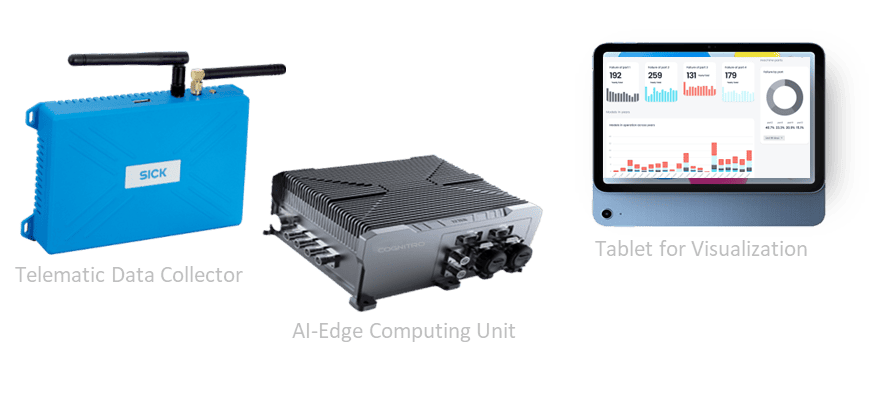
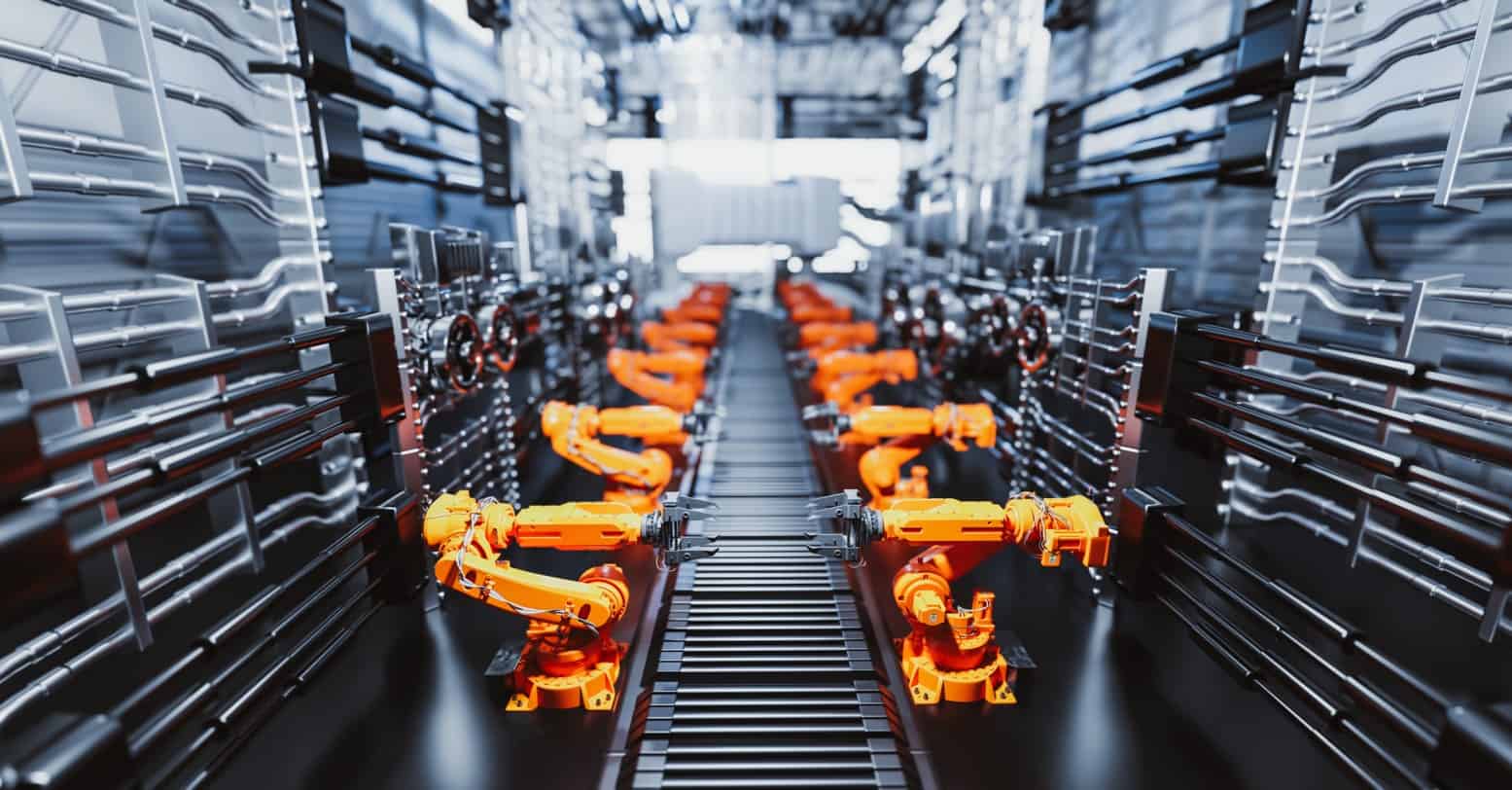
Potential Solutions Benefits
Return on Investment
Operation Efficiency
Reduction of the number of parts experiencing less downtime
Model Prediction Accuracy
The ratio by which the model hits or misses the target prediction
Machine Downtime
Total hours saved for maintainance and troubleshooting per week